Pharmaceutical Industry
Machine vision in the pharmaceutical industry plays a crucial role in ensuring product quality, regulatory compliance, and operational efficiency. By leveraging cameras, sensors, and advanced image processing algorithms, machine vision systems can inspect, monitor, and control various stages of pharmaceutical manufacturing, packaging, and distribution. Here are the key uses and benefits of machine vision in the pharma industry:
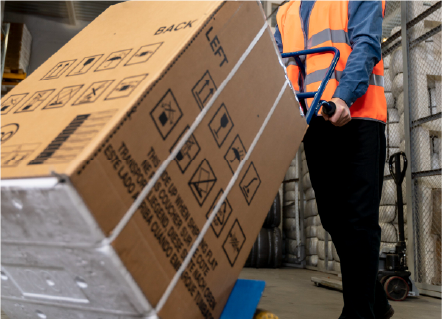
Key Uses of Machine Vision in the Pharmaceutical Industry
Product Inspection and Quality Control:
Tablet and Capsule Inspection: Machine vision systems are used to inspect tablets and capsules for defects, such as cracks, chips, or irregular shapes. High-resolution cameras can detect small imperfections that may not be visible to the human eye, ensuring only high-quality products reach the market.
Visual Inspection of Packaging: Vision systems can check the integrity of packaging, ensuring labels are applied correctly, seals are intact, and barcodes or QR codes are readable. This is critical for preventing packaging errors that could lead to contamination or misidentification of products.
Fill Level and Seal Inspection: Machine vision can verify the fill levels of bottles, vials, and other containers. It can also inspect the integrity of seals and closures, ensuring that products are securely packaged and preventing potential leaks or contamination.
Labeling and Serialization:
Label Verification: Vision systems verify that the correct labels are applied to products during the packaging process. This includes checking for correct text, logo placement, and the absence of errors like missing or misaligned labels.
Track and Trace: Machine vision plays a key role in ensuring that serialization codes (such as barcodes, 2D matrix codes, and RFID) are correctly applied and readable. This enables regulatory compliance, facilitates supply chain tracking, and helps prevent counterfeiting.
Barcode Scanning: Automated systems use machine vision to read and verify barcodes on packaging, which is vital for managing inventory and ensuring accurate distribution of pharmaceutical products.
Compliance and Regulatory Inspection:
Regulatory Compliance: Pharmaceutical manufacturing is highly regulated, with strict requirements for quality control, traceability, and safety. Machine vision systems ensure compliance with Good Manufacturing Practices (GMP) and other regulatory standards by automating inspections and reducing human error.
Real-time Monitoring: Vision systems can continuously monitor production processes to ensure that they adhere to regulatory guidelines, such as FDA or EU standards. Any deviations can trigger alerts for immediate corrective actions, ensuring products meet the required specifications.
Contamination Detection:
Foreign Particle Detection: Machine vision is used to identify foreign particles or contaminants in products. This is critical for maintaining the sterility of pharmaceutical products, especially for injectables, eye drops, and other sterile formulations.
Visual Checks for Cleanliness: Vision systems can inspect the cleanliness of equipment, packaging lines, and containers to detect any residual contamination, ensuring that products are manufactured in a hygienic environment.
Automated Sorting and Handling:
Sorting and Counting: Machine vision systems can sort products based on size, shape, or other criteria, ensuring they are placed in the correct packaging. They can also automate counting, ensuring that each package contains the correct number of tablets, capsules, or vials.
Inspection of Pill Bottles and Containers: Vision systems can inspect the contents of pill bottles and other containers to ensure that the proper quantity of tablets or capsules is present and that they are in good condition.
Process Optimization and Efficiency:
Speed and Throughput: Machine vision systems can operate at high speeds, allowing for faster production rates without sacrificing quality. This is especially important in high-volume manufacturing settings where human inspection would be too slow.
Predictive Maintenance: Vision systems can monitor the condition of equipment on the production line, identifying early signs of wear or malfunction. This allows for proactive maintenance, reducing downtime and preventing costly repairs.
Detection of Labeling and Packaging Errors:
Packaging Integrity: Machine vision systems can detect issues such as underfilled or overfilled bottles, misapplied caps, incorrect packaging materials, or damaged packaging. These checks ensure that only properly packaged and labeled products are shipped to customers.
Date and Lot Code Verification: Vision systems can ensure that date codes, batch numbers, and expiration dates are correctly printed and visible on packaging. This is critical for tracking product safety and compliance with shelf-life requirements.
Inspection of Injectable Products:
Inspection of Vials and Syringes: Machine vision is used in inspecting injectable products like vials, syringes, and ampoules for particulates, cracks, or glass defects. Ensuring the sterility and integrity of injectable pharmaceuticals is essential for patient safety.
Benefits of Machine Vision in the Pharmaceutical Industry
Improved Product Quality:
Machine vision ensures high levels of consistency and accuracy in inspections, reducing the chances of defective or contaminated products reaching the market. This is critical for maintaining the safety and efficacy of pharmaceutical products, which directly impacts patient health.
Increased Efficiency and Productivity:
Automated visual inspection reduces the need for manual checks, speeding up the production process and increasing throughput. This leads to higher operational efficiency and allows for better utilization of resources, ultimately reducing production costs.
Enhanced Compliance and Traceability:
Machine vision plays a vital role in maintaining compliance with stringent regulatory requirements. By ensuring accurate labeling, serialization, and documentation, machine vision helps pharmaceutical companies meet industry standards such as FDA, EU regulations, and the Drug Quality and Security Act (DQSA).
Serialization and track-and-trace systems powered by machine vision allow for better control over the supply chain, helping to prevent counterfeiting and diversion of pharmaceutical products.
Reduced Risk of Human Error:
By automating repetitive and high-precision tasks, machine vision systems minimize the risk of human error, which can lead to costly product recalls, legal liabilities, or damage to a company's reputation.
Cost Savings:
While the initial investment in machine vision technology may be high, the long-term savings from reduced waste, fewer product defects, faster production times, and lower labor costs can be significant. In addition, reducing recalls and improving product consistency contributes to cost savings and brand trust.
Real-time Monitoring and Data Analytics:
Machine vision systems can collect real-time data on production processes, which can be used for ongoing performance analysis, troubleshooting, and process optimization. This data-driven approach allows for continuous improvement in manufacturing practices.
Faster Time-to-Market:
With automated inspections and streamlined packaging processes, pharmaceutical companies can reduce the time it takes to bring products to market, improving competitiveness and responsiveness to market demand.
Minimized Product Recall Risk:
By catching defects early in the production line, machine vision helps minimize the risk of product recalls due to quality issues, ensuring that only products that meet strict quality standards are shipped to customers.
Improved Safety and Hygiene:
Vision systems can detect contamination, foreign particles, and cleanliness issues, ensuring that pharmaceutical products are produced in sterile and safe conditions. This is particularly important for injectable drugs, ophthalmic products, and other critical therapies.